実践型研修B2
COURSE B2
「生産現場改善の匠」実践研修(2日間コース)
改善の基本を理解して、様々な現場改善手法を習得し実践に繋げる
スタイル |
対面型研修 |
---|---|
対象者 |
ものづくり現場リーダー・生産工程改善技術者 |
研修期間 |
6H×2日 |
最適定員 |
12人 |
研修の狙い |
生産性向上を展開するための改善手法を習得するコースです。改善の考え方、改善の原理/原則、IEを中心とする改善手法を講義、演習、動画分析により理解して、生産現場で実践できるようにすることを狙いとします。 |
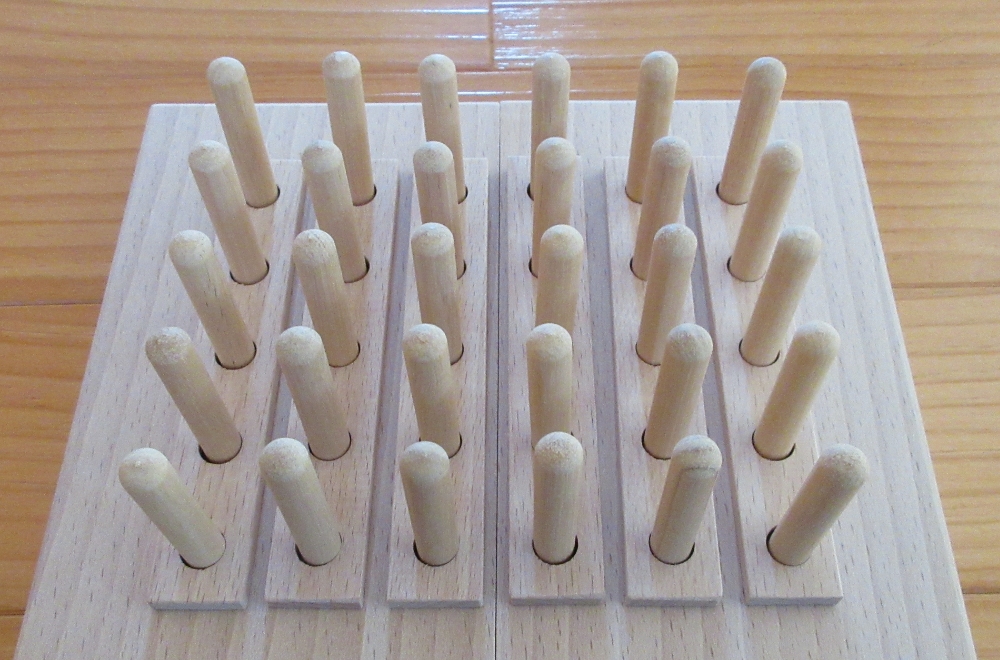
日程 | 研修項目 | 主な内容 |
---|---|---|
1日目(6時間) | 【第1章】 改善の考え方 |
1, 改善活動の進め方 ①ものづくり力の向上 ②ムダを見つけるために ③改善活動の基礎作り |
【第2章】 改善の原則 |
1, 動作経済の原則 ①動作経済の原則とは! ②演習1:ボルト組み付け作業ムダ取り検討 ③演習2:チラシ折りムダ取り検討(動画分析) 2, ECRSの原則 ①ECRSの原則とは! ②演習1:ワーキングマザーの時短検討 ③演習2:キャベツ切りのムダ取り検討 |
|
【第3章】 改善の基本 |
1, 究極5S 1-1:究極5S 1-2:5Sの基本 ①5Sの捉え方とその本質 ②5Sの基本 ③演習1:写真から5S改善検討(パーツ棚) |
|
【第4章】 改善の基本 |
2, モーションマインド ①演習1:ピンボード組立作業分析(モーションマインド・標準時間) 3, 7つのムダ ①7つのムダ ②ムダの見つけ方 ③ムダ取りのアイデア 4, 目で見る管理 ①目で見る管理の必要性・条件 ②目で見る管理の事例 ③演習1:生産進捗管理板検討 |
|
2日目(6時間) | 【第5章】 現場改善手法1 |
1, ボトルネック改善 ①ボトルネックとは! ②ボトルネックの徹底活用と強化 ③演習1:機械部品加工ラインの改善 2, 連合作業分析法 ①必要数でタクトを決める ②標準作業組み合わせ票の活用の仕方 ③演習1:プレス作業工程のムダ取り検討 |
【第6章】 現場改善手法2 |
3, 要素作業分割 ①要素作業分割とは! ②作業時間分析の仕方/手順 ③演習1:要素作業分割・時間分析 4, ラインバランス改善 ①ラインバランス改善の進め方 ②ラインバランスの評価 ③最適作業ステーション数の算出 ④演習:梱包工程のラインバランス改善 5, 作業動作分析手法 ①MODAPTS法の基礎理論 ②演習1:動作分析 ③演習2:製造ラインの課題抽出と対策 6, 各種改善手法(改善事例) ①改善の着眼点と抽出方法を事例から学ぶ ・5S三定 ・セル生産 ・なぜなぜ分析からのニンベンのある自働化 |
CONTACT